自社開発技術
株式会社KDAが開発した新しい技術のご紹介です。
産業界のニーズにお応えする自社開発技術
-
スマートボットミーリング®
ロボット導入による自動化によって国産のクオリティを維持しつつも海外製に並ぶ低価格化を実現。
完全自動化による24時間稼働により生産性大幅に上げ、納期の短縮を実現。
-
SMART MOLDING®
プラスチック成形をもっと簡単にして、低価格化したい。 というニーズから生まれた技術。
型代が従来の3分の一! 経済的メリットに加え高品質をもご提供します。
-
NEAR NET MOLDING®
スーパーエンプラをペレットから簡易成形し、細部はマシニング加工で仕上げる「ハイブリッド加工」。
PEEKやPPSU、PEIなど、無駄を省いて低価格化を実現しました。
-
樹脂と金属の直接接合
プラスチックと金属の直接接合、接着剤やボルト止めなど一切無し。 PEEKと金属の接合は弊社オリジナルです。
接着材による接合力不足や成分溶出などの問題を克服した技術です。
-
ワンプロセッシング2by2®
同じ形状を同時に4個加工。 総合加工時間を削減し、コストダウンを狙う工法です。
主に、板材からの2次元加工に向いています。
KDAの技術開発のコンセプト
① 工程の最適化 (複雑、過剰な工程を、簡単に短くする。)
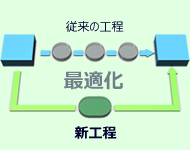
「もっと簡単にできないか?」
手間と時間がかかる複雑な工程。 改めて検討してみると、ちょっとした工夫で簡単にできたり、工程をまとめることができたりします。
工程を最適化することによって、時間の短縮、作業者の注意力の安定化、延いては品質の向上、コストの削減につながります。
② 材料の最適化 (材料の無駄を抑える!)
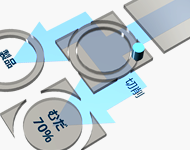
「材料の廃棄がもったいない。」
実際に材料を切削して廃棄される部分はかなりの量になります。 左の図のような形状の製品の製造過程では、約70%の部分が無駄になります。 スーパーエンプラなどの高価な材料は、無駄が多いと製品単価が高くなってしまいます。
「如何に材料の無駄を抑えられるか」という視点をもって開発を進めています。
③ 品質の最適化 (品質は落とさず、向上させる。)
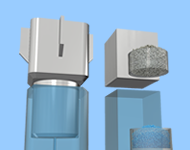
「高品質のものを低価格化したい。」
寸法精度においても、製品材質においても、より良いものを求めて開発をしています。
一般的に高品質になると製品価格も高くなりますが、精度のメリハリや、上記の工程・材料の最適化をもって「高品質で低価格」を実現できるよう努めています。