KDAのトピックス・お知らせ
KDAに関する最近の新しいニュース、お知らせを掲載いたします。
- HOME
- トピックスTOP
- アーカイブ2009TOP
- 2009.07.30
工業調査会「M&E」誌に社長トップインタビュー
理工学関連の専門的出版を行う出版社、(株)工業調査会の月刊誌「M&E」に、(株)KDAの木田行則社長のインタビューが掲載されました。
タイトルは、「創意工夫のオンリーワン技術でグローバル展開~ジャストインメイクと3Dスリップキャスト法~」。 以下、A4版の見開き2ページ分の内容です。
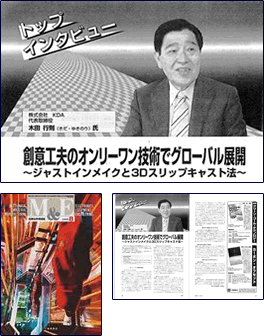
不況のさなか、円高もあり日本の製造業界が揺らいでいる。そして、毎日、マスコミでは不景気であることを言わない日は無い。だが、日本の製造業の底力は伊達ではない。オンリーワン技術を持つ企業は、不景気であっても強いのである。
今回は、そんなオンリーワン技術を追求して、注目を浴びているKDAの代表取締役木田行則氏にお話を伺った。
<木田行則氏の横顔>
出身地 愛知県
明治大学 1965年卒
樹脂加工業界では、初めて光造形を導入し、現在、RP(光造形)産業協会副会長をも務める。
また、樹脂加工技術をセラミックス分野に展開し新工法を開発。更に樹脂加工分野においても独自の製法を考案。
オンリーワン技術の追求
-ジャストインメイクとは?
木田氏 ジャストインメイクとは、はじめは成形、仕上げを切削加工という樹脂のハイブリッド加工のことで、そのものをズバリ作りたいという動機とインスピレーションから名付けた製法だ。プラスチックペレットから最終形状に近いブロック体を作り、切削加工して完成。プラスチックの成形工程に精密な金型を使用しないため、コストを抑えることができる。さらに、これまで型製造にかかった期間も省くことができる。ABS、ウレタン、光造形ではない製品材質のペレットでモデル試作が可能だ。スーパーエンプラにも対応している。高級材料であるスーパーエンプラは、一般的に材料・丸棒材よりペレットの方が安く、また製品形状に近い成形を行うため、切削部分が少なくなり、コスト削減に大きく貢献する。一見、容易そうに思われるが、当社が業界史上初めて実現した。
-どのようなメリットがあるのか?
木田氏 大きく分けて試作と少量生産と二つの用途がある。試作からいうと、昔は木とか粘土でやっていた。その次は、ABS樹脂で切削して、貼り付けてやっていた。次は光造形が出てきた。これらは、いずれも材質が最終製品のものとは違う。当社の特長は最終製品の材質で試作ができるのが、一番のメリット。本番材質の試作で直ぐに最終試験ができるため、開発期間が大幅に短縮する。
次に少量生産だ。一般製品は、何十万個、何百万個と大量に作る場合は射出成形で作るが、年間100~500個くらいしか作らないものも世の中には一杯ある。そういうものは、金型つくらず、うちの製法でできる。既存の製法では、この材質が良いということになっても、その素材で作る方法が無かった。金型を作って射出生計で作らざるをえなかった。うちのものは、一個から最終製品と同じ材質で作ることができるというメリットがある。これまでの製品開発は、代替材であるABSやウレタンなどで試作を行ってきたが、試作段階からペレットで作れるようになると、開発工程がかなり効率化される。
-3Dスリップキャスト法とは?
木田氏 当社が開発した新しいセラミック加工法で、加工しにくくコストがかかるセラミックスを、効率よく、あらゆる複雑な形状にも対応し、しかも低コストで製造できるように考えられたセラミック工法だ。オリジナルのセラミック工法でネジの形を900~1000種くらい規格化して、売っている。単純に、どろどろにしたものを型に流すだけ。何が違うかというと、どろどろにしたものを形につくるのは、例えば、お茶碗とかあった。石膏の型に流してね。そうすると、石膏が水分を吸って壁にくっつく。そして適当な時間であける。そうすると、時間が長ければ、厚みが厚くなり、短ければ薄いものができる。乾いた段階で焼けば、できるという製法がある。そういう製法だと、吸うから長く置いても真ん中が空洞になる。当社は、のりを開発した。それを使用すると、無垢のものができる。ほんのちょっと、のりを入れることで、密度が上がるという製法を開発した。のりが最大の秘密だ。セラミックのネジは、削り出しでやっているところもあるが、うちの製法の方が削り出してないから亀裂が入っていないので強度がある。型に対する固定的な概念がない。その形状を作るために有用であればどのような素材でも型として使用する。当社では、多くのマシニングセンタを使い、プラスチックより型を製造している。複雑なものになると、光造形によって型を製造する場合もある。ロストワックスという手法を用いて、特殊形状を製造する場合もある。金型を用いず、安い樹脂型などを用いることが大きなコストダウンになる。機械加工や成形でも難しいことが大きなコストダウンになる。機械加工や成形もで難しい複雑形状・微細形状・3次元形状などの製造に最適だ。
頭の中で理屈があればできる
-どこでもやっていない部品をやっていますね
木田氏 30年前は、公害問題が社会で表面化したところで排ガス処理装置を自社開発し、製造販売を手掛けてみたが、30才前の若輩者では商売の方法も技術も薄く儲かるどころか継続してゆくことにも苦慮した。そこで、部品だけを加工する受託加工に切り替えた。しかし、汎用品の部品はコストも下落してゆく中で、弊社にある光造形技術を生かして、特に試作品に注視しどこでもやっていないオンリーワンの商品を目指した。
-独自の製品を開発する秘訣は?
木田氏 私は、理屈には合わないことは、常に疑問符を持つ。頭の中で値靴が成立すれば絶対にできると考える。今まではやり方が間違っていると。出来ないものをやるのではなく、誰も気づかないものをやる。私が発明するのではなく、理論的にはできるが、使われていないものを探す。新しいものを開発するわけではない。アインシュタインみたいな天才じゃない。ちょっとしたアイディアなのよ。がり勉は絶対駄目だ。知識に頼るのではなく、創意工夫が大事。
中国に売るものを作ればいい
-中国の脅威は?
木田氏 私は、以前から中国がどんどん発展してくれて良いと言っていた。人件費が安いところには適わない。ロボットで製造していてもそう。完全に無人と言うことはないんだから。中国が日本に追いつくのに何年かかるか分からないが、それまでは、中国に売るものを作れば良い。以前は、中国に産業が移転するということが言われたが、最近はそれを言わなくなった。中国に売れるものはないか、ないかと言われる。売れるものが絶対にあるはずだ。
-今後は?
木田氏 社会全般に、会社の営業活動は交際費の有効活用に依存した時代が去り、全ての会社がサービスやコストのスピード化時代となった。当社は最上の技術と良品安価を前面に勝負に出る。そして、オンリーワンを追求して社会に貢献したい。
2009年7月30日